ELECTRICAL MAINTENANCE SERVICES
‘’HYPOXY SYSTEMS, INC,’’ U.S.A., one of the leading MRO EPOXY SOLOUTIONS provider & a premiere formulator, manufacturer and worldwide marketer of quality epoxies.The company is headquartered at South Carolina USA & with the completely automated modern manufacturing facilities, provides internationally proven Metal & Ceramic filled Polymer compounds for maintenance & repair solutions.
The products are regularly used worldwide for planned / preventive maintenance, emergency repair & Plant / Components efficiency enhancement applications in varied industry segments like Power generation, Power Transmission and distribution, Mines & minerals industry, Steel plants, Cement plants, Oil & gas, Petrochemical & refineries, Chemical & fertilizer, Aviation industries etc.
We offer the complete ‘’ HyPoxy ‘’range of products & are equipped with strong nation wide
presence of techno commercial executive and managers, Team of skilled applicators along wide
network of authorized dealers located at strategic locations.
We also provide complete MRO services like Maintenance survey, assessment of problems,
Recommendation of suitable products and services & finally the complete application services.
We also provide timely feedback with the data on financial savings by customers employing our
services.
Some of the Common Applications / Jobs being attended by us with various ELECTRICITY BOARDS in POWER TRANSMISSION & DISTRIBUTION segment are - :
- On line transformer oil leakage arresting in power and distribution transformers from various locations like radiator fins, buckolz relay, radiator main flange, Transformer parting plate, Transformer Top plate, Ruptured & cracked gaskets, Welding joints etc.
- On line transformer oil leakage arresting from Bushing area.
- In situ repair of damaged or broken petticoat area of Insulators & Isolators.
- Insulator coating by Ceramic Hard Coat to improve glaze & creep resistance.
- Inside substation bus bar coating.
- External open / naked bus bar coating.
- Jumpers coating.
- HT & LT Bushing dielectric coating.
- Bus bars sprouts and supports coating by ceramic hard coat to prevent moisture absorption.
- Epoxy moulded CT / PT coating by Ceramic hard coat to prevent moisture seepage.
Hy Poxy range of repair compounds are mostly 2 component systems consisting of the RESIN &
HARDNER. The resin contains of finely powdered metals or ceramic suspended in an epoxy filler. The
hardner is a chemical curing agent. When the resin and the hardner are mixed in the right
proportions, the mixture quickly cures to form the solid mass.
Hy Poxy products are engineered to carry out fast insitu repairs and put damaged equipments back
into service quickly.The cured metallic mass will have comparable and often superior physical and
chemical properties as compared to base metal.
We at HyPoxy supply the material to attend the above applications to electricity boards and are
also provide application and job completion services through our nation wide service team.We
have also formulated special kits containing the required material to attend the above applications.
Some of the large jobs, we attend by supplying the material after inspection and then depute our
service team for application services.
We also provide the free training to board technical personnel for using the products and attend the
above applications independently.
Salient features & benefits -
- Wide Range – The complete range of Metal filled, Aluminium, Titanium & Ceramic filled liquids and putties to address complete Maintenance needs of indian industry.
- Various Pack Sizes. – We have small, medium & large pack sizes for all our products, which gives customers the benefits of flexibility in selection of suitable pack sizes as per their requirements.
- Fast curing 5 minutes Aluminium putties in various pack sizes.
- In Hy Poxy products, the fillers are closely linked with high molecular weight polymer binders. This ensures better and higher tensile shear adhesion strength over equivalent products from competition.
- Hy Poxy products cures faster & reaches to maximum strength in minimum time ensures reduced down time.
- Hy Poxy products have lower water permeability. This ensures better performance when they are exposed or immersed in water.
- When the cured compound is exposed to heat / temp. – dry or wet, the mechanical properties such as Flexural strength, Compressive strength, Tensile shear adhesion strength and Hardness drops at elevated temp. The rate of fall is more steep in competition products than ours. This indicate better suitability / Retainability of mechanical properties at elevated temp in our products.
- Our every hardener pack is nitrogen sealed for safety, pilferage & long usable life.
- Nromally our products exhibits long shelf life of approx 5 years if stored well.
- We ensure that Hy Poxy products supplied to customers are not more than 5-6 month old from manufacturing date. This ensure customer to enjoy complete 5 years period of ‘’BEST BEFORE USE‘’
BUS BAR INSULATION, JUMPER COATING, SPROUTS & BUSHING COATING, EPOXY MOULDED CT / PT COATING
The bus bar flash over due to rat and lizards, Loss of glaze on insulator and bushings, Moisture absorption by Bus bar sprouts are the common problems faced by all the substation maintenance personnel. HY POXY SYSTEMS INC. OF USA offers a time tested unique solution to address above issues.
PROBLEMS- :
- SUB STATION INTERNAL BUS BARS & OPEN NAKED BUS BARS COATING.
- SPROUTS & BUSHING COATING.
- HYPOXY MOULDED CT / PT COATING
In the inside panel bus bars the flashover is a normal phenomena when external objects like rat, lizards
goes inside. Similarly monkeys are the common cause of flash over in the outside open bus bars.
The flash over leads to -:
- No Power situation.
- Loss of revenue for the board.
- Expensive maintenance to bring back the normal situation.
Bus bar sprouts normally absorbs the moisture during the rainy seasons & due to this their IR value
goes down. This normally makes flash over in the bus bars as the bus bars are mounted on this
component.
Outside mounted bushing normally loose the glaze due to continuous exposure to heat / water & dust.
Due to above sometimes very heavy pitting are also observed. This leads to IR value of the bushing &
sometimes also lead to sparking and flash overs.
The epoxy moulded CT /PT normally mounted outside absorbs the moisture in the rainy seasons. This
brings down the IR value of the component & leads to flash over.
THE HYPOXY SOLUTION-:
Many solutions have been tried out but with limited success and each solution have many limitations.
The Hy Poxy solution is a quick and easy solution and does not involve cumbersome procedures.
The Hy Poxy solution is consisting of three main products
- Hy Poxy ‘’CLEANER / CONDITIONER’’
- Hy Poxy ‘’WEAR RESISTANT PUTY’’
- Hy Poxy ‘’CERAMIC HARD COAT - RED’’
The Hy Poxy ‘’CERAMIC HARD COAT - RED’’ is a normal curing product which has property of high dielectric strength ( 16KV / mm ) with very good heat dissipation properties.
BRIEF PROCEDURE -:
- Clean and roughen the area using the clean cloth and emery paper.
- Clean and prepare the surface using the Cleaner / Conditioner.
- Make a steel template with same contour & external dimensions as of original disc.
- Mix small qty of Hy Poxy ‘’WEAR RESISTANT PUTY’’ as per the mixing ratio advised.
- Apply by spatula the mix material & align to match the template contour.
- Mix more material and fill all the area.
- Allow the deposit material to cure as advised in the product technical spects.
- Once the Wear resistant putty is cured ,mix small quantity of Hy Poxy ‘’CERAMIC - RED’’
- Apply by brush. The Ceramic coat is self settling hence slowly flow and set evenly.
TRAINING:- -::The operating staff of a substation can be easily trained to apply these products in case of emergency requirements. Hy Poxy Systems also offers special training courses for group of operating and maintenance personnel from SEB.
The company offers application services through nation wide presence of techno commercial executive and managers, Team of skilled applicators along with wide network of authorized dealers located at strategic locations.
We provide complete MRO services like Maintenance survey, assessment of problems, Recommendation of suitable products and services & finally the complete application services. We also provide feedback with the data on financial savings by customers employing our services.
TESTIMONIALS:-The above products and methods are in extensive use in the main and sub stations of various
electricity boards and also private power companies.
We can submit few case studies, performance certificates along with job completion reports and job
photographs on demand.
INSITU INSULATOR REPAIR
Due to flashover, the bursting of Insulators and breakage of Insulator petticoat area is a common
problems in any sub station.
Normally replacing the broken disc is the only solution in the hand of maintenance personnel but
which is very tedious and time consuming. Some times in high voltage substations, the replacement
takes few days which leads to shut down of the substation.
HY POXY SYSTEMS INC. OF USA offers a time tested unique solution to address above issues.
PROBLEMS:-
INSITU REPAIR OF PETTICOAT AREA OF INSULATOR DISC.
Due to flashover or high voltage surges or due to loss of insulator glaze, some times the petticoat
area of insulator is bursted and broken.
In the normal course, the replacement of the broken disc is the obvious answer. But this option
normally is very time consuming and expensive too.
The replacement of disc calls for complete sub station shut down, dismantelluing of the insulator
and finally the replacement of broken disc.
This leads to -:
- No Power situation.
- Loss of revenue for the board
- Expensive maintenance to bring back the normal situation
THE HYPOXY SOLUTION -:
Many solutions have been tried out but with limited success and each solution have many limitations.
The Hy Poxy solution is a quick and easy solution and does not involve cumbersome procedures.
The Hy Poxy solution is consisting of three main products
- Hy Poxy ‘’CLEANER / CONDITIONER’’
- Hy Poxy ‘’WEAR RESISTANT PUTY’’
- Hy Poxy ‘’CERAMIC HARD COAT - RED’’
The Hy Poxy ‘’CERAMIC HARD COAT - RED’’ is a normal curing product which has property of high dielectric strength ( 16KV / mm ) with very good heat dissipation properties.
BRIEF PROCEDURE -:
- Clean and roughen the area using the clean cloth and emery paper.
- Clean and prepare the surface using the Cleaner / Conditioner.
- Make a steel template with same contour & external dimensions as of original disc.
- Mix small qty of Hy Poxy ‘’WEAR RESISTANT PUTY’’ as per the mixing ratio advised.
- Apply by spatula the mix material & align to match the template contour.
- Mix more material and fill all the area.
- Allow the deposit material to cure as advised in the product technical spects.
- Once the Wear resistant putty is cured ,mix small quantity of Hy Poxy ‘’CERAMIC - RED’’
- Apply by brush. The Ceramic coat is self settling hence slowly flow and set evenly.
TRAINING:- -::The operating staff of a substation can be easily trained to apply these products in case of emergency requirements. Hy Poxy Systems also offers special training courses for group of operating and maintenance personnel from SEB.
The company offers application services through nation wide presence of techno commercial executive and managers, Team of skilled applicators along with wide network of authorized dealers located at strategic locations.
We provide complete MRO services like Maintenance survey, assessment of problems, Recommendation of suitable products and services & finally the complete application services. We also provide feedback with the data on financial savings by customers employing our services.
TESTIMONIALS:-The above products and methods are in extensive use in the main and sub stations of various
electricity boards and also private power companies.
We can submit few case studies, performance certificates along with job completion reports and job
photographs on demand.
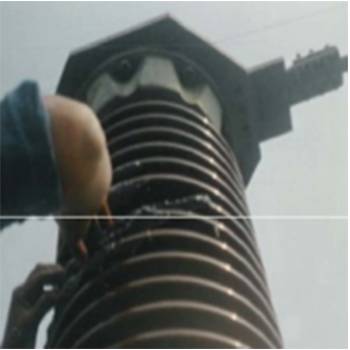
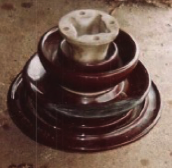
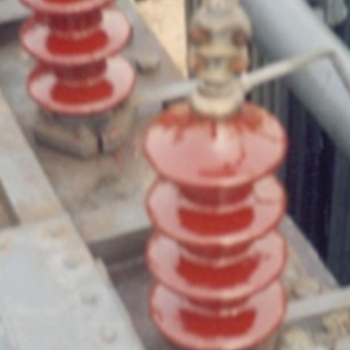
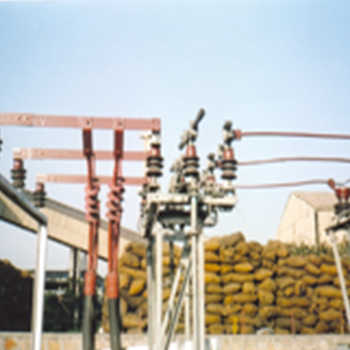
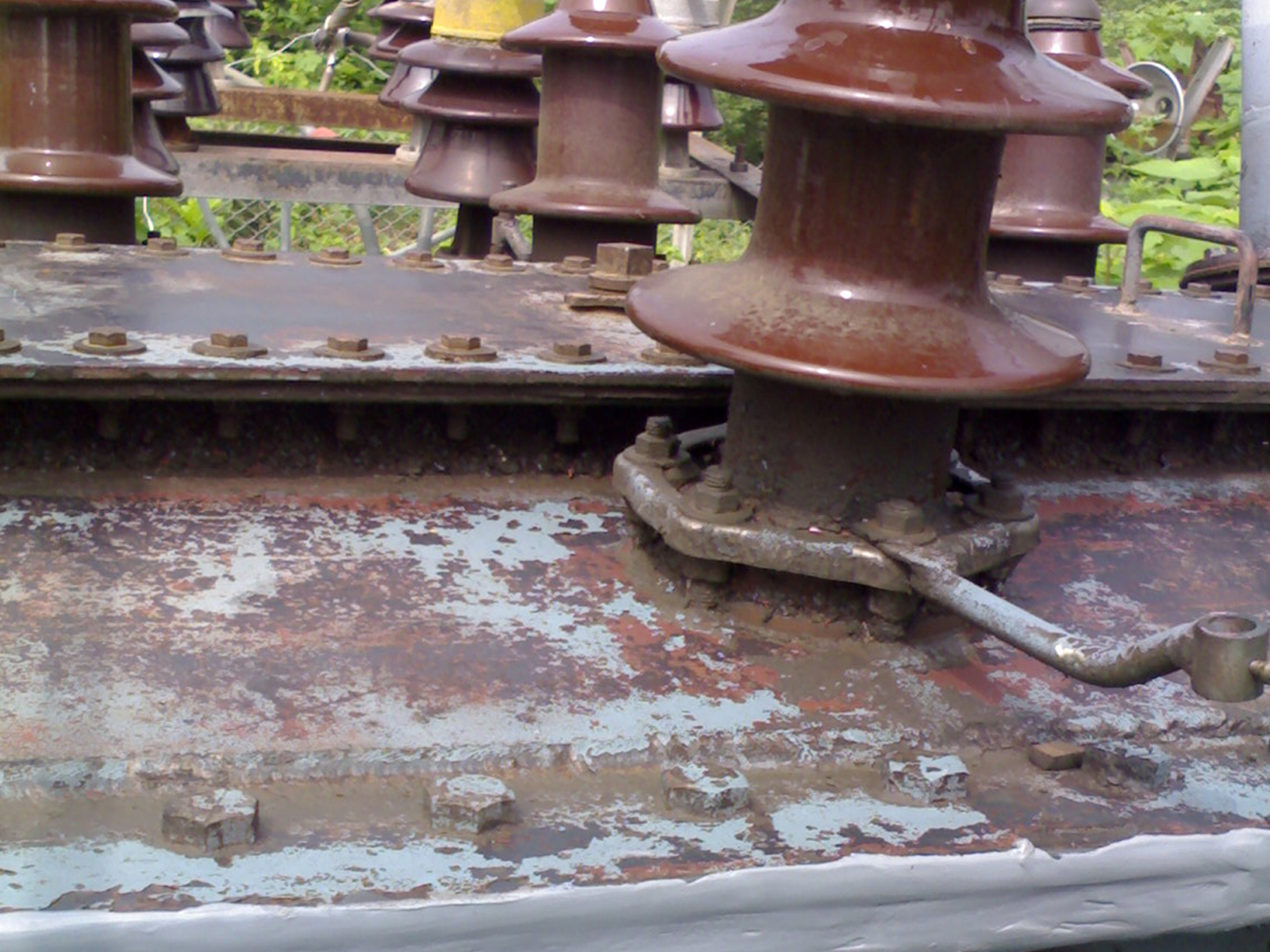
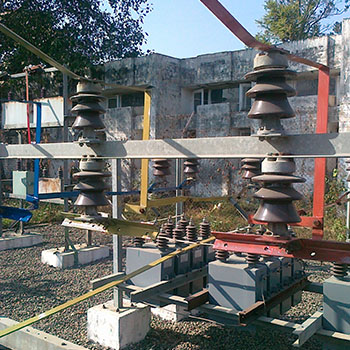
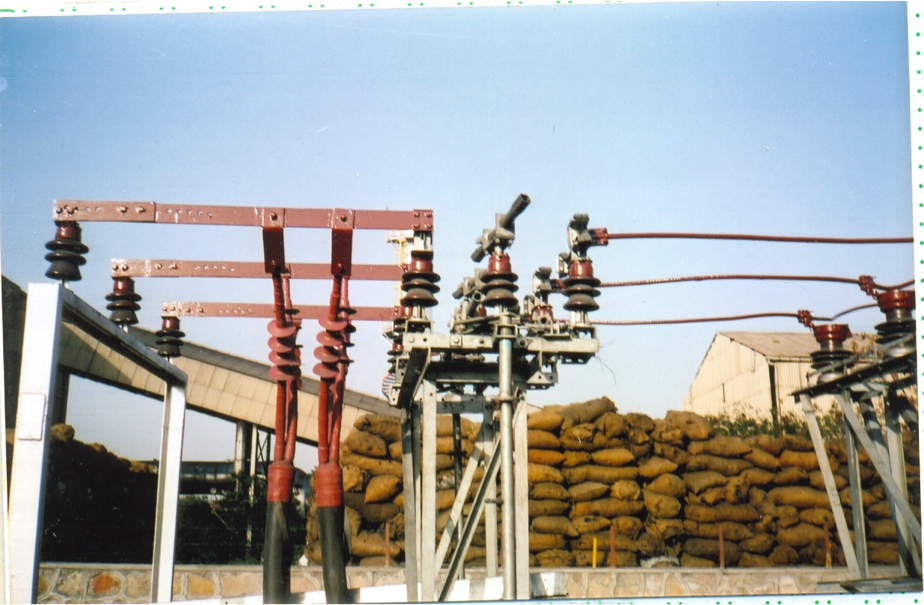
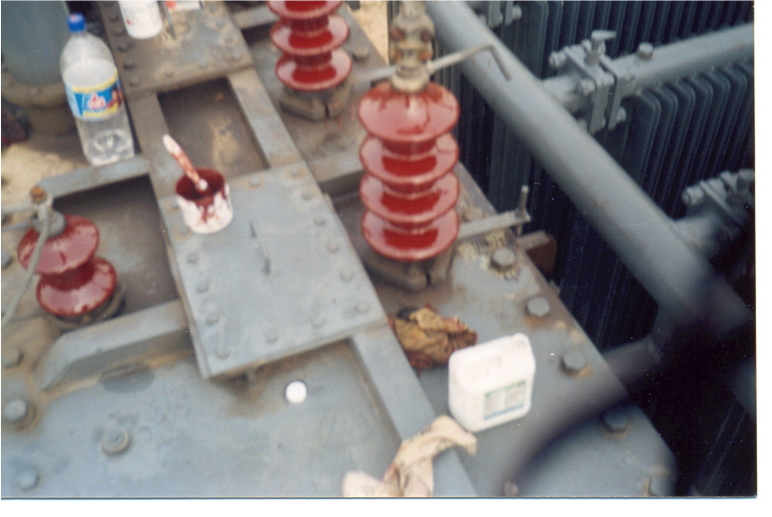
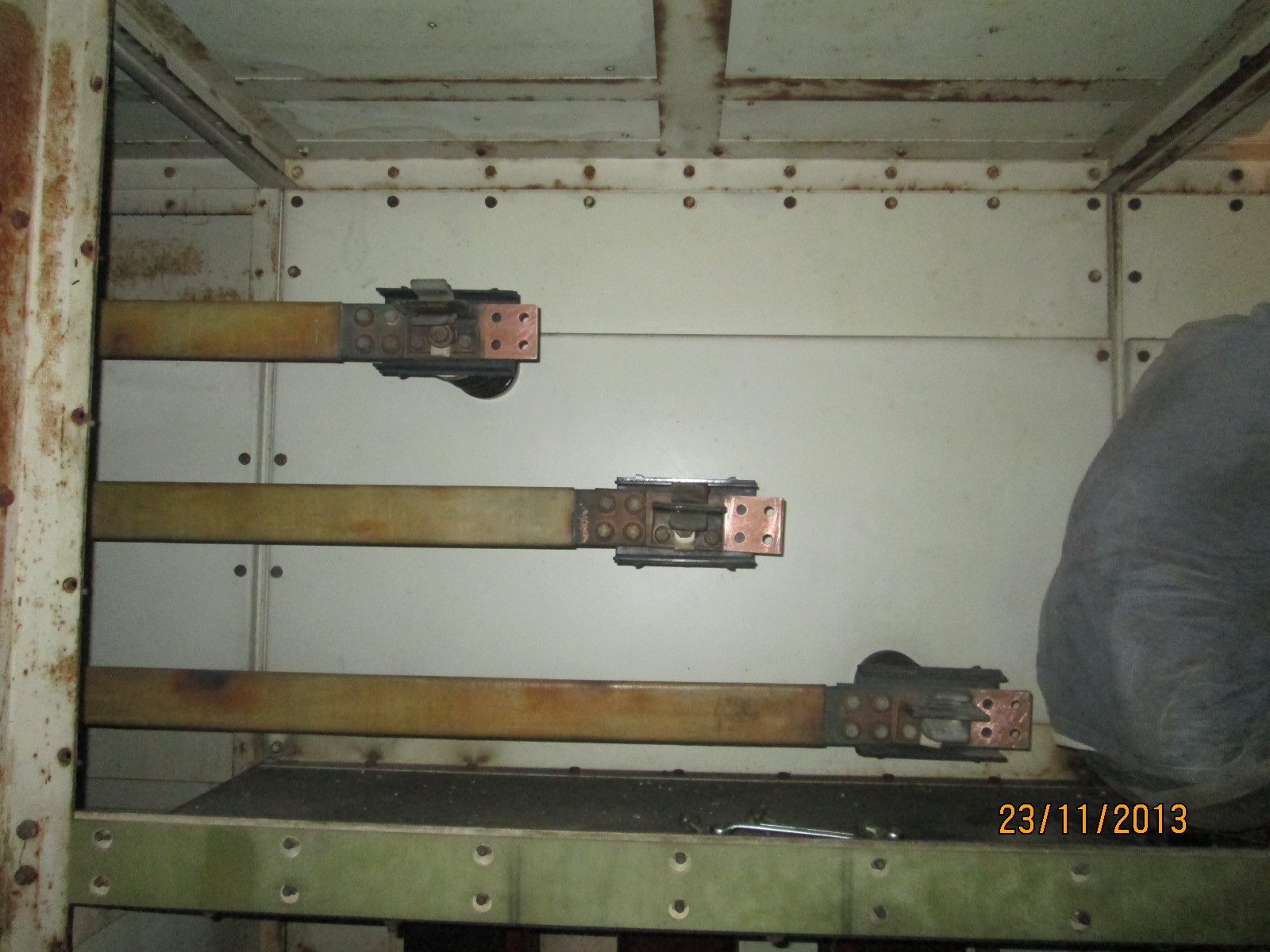
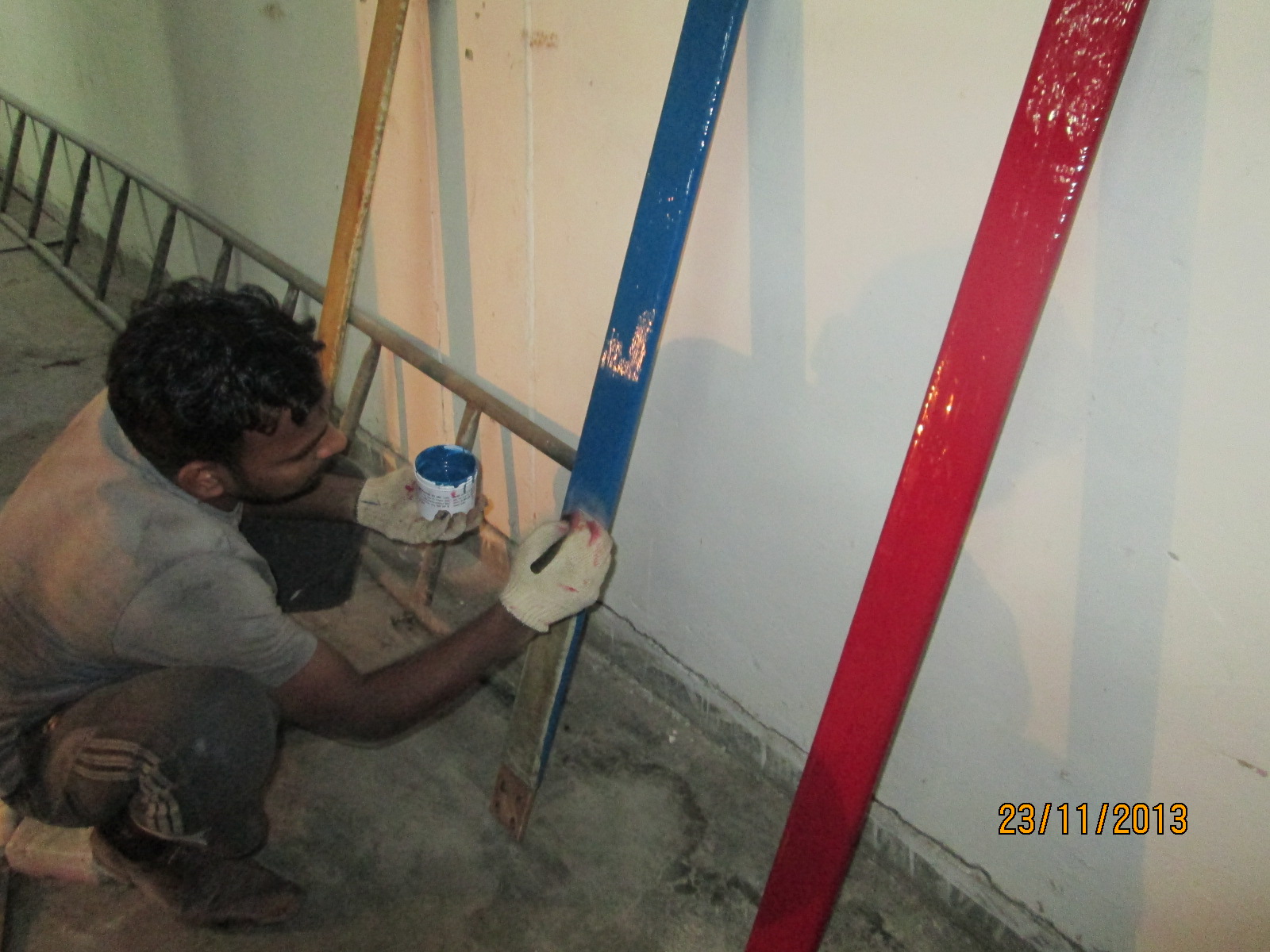